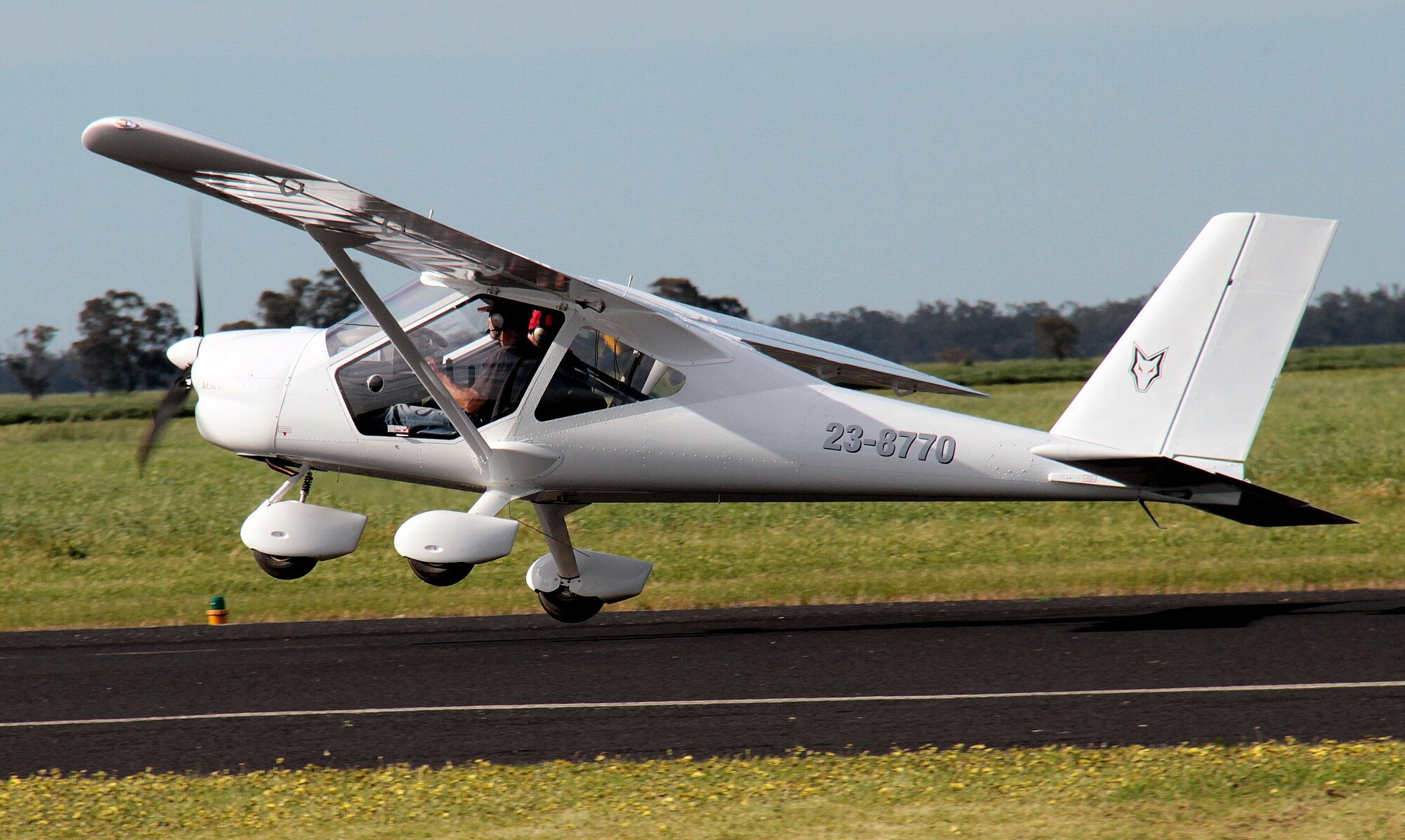
Ballooning & floating on landing?
Probably the most common comments we get from student pilots – and quite a few experienced pilots too – are about their perceived skills needed to land a light sport/recreational aircraft. In many cases, pilots make comments like: “I pulled back on the controls to flare and the aircraft just ballooned” or “it just seems to float and float along the runway; it just doesn’t want to land”.
Both of these events when landing an aircraft – ballooning and floating – have their own dangers for the pilot, which if not anticipated and handled correctly can result in a bent aeroplane…or worse. So here are a few tips on how to get it right.
In simple terms, almost all balloons and floats during landing are caused by excess speed over the landing threshold. Unfortunately, many instructors have a habit of telling their students to add 5 or 10 knots to their approach speed ‘for safety’. In reality, they are often actually reducing the margin of landing safety by doing so. And this habit of adding speed to the book figure becomes instilled as a very hard-to-break habit. My own pilot training, now many many years ago, involved adding approach speed in certain circumstances and, even now, I have to fight the impulse to add speed when landing in the A22LS Foxbat, Kelpie and A32 Vixxen.
Let’s go ballooning
So, what’s wrong with more speed? There are two main reasons but first, remember light sport and recreational aircraft are very low weight (read: low inertia) aircraft. So, like a small car, these types of aircraft will change direction much more quickly than a limo, a ute or a truck. Not that I’m suggesting your average Cessna/Piper etc are trucks…. As a result, when landing, the controls are much more effective than bigger GA aircraft and to much lower airspeeds. At only slightly faster speeds the controls are even more powerful, so if you are too fast when you pull back to flare, the aircraft will not just flare, it will start to climb again, even with the engine at idle. This is called ‘ballooning’. When you go ballooning, the impulse is to push the nose down to reduce the sudden climb. Unless you are very quick (and/or experienced) you’re likely in for a bent nose leg and/or busted propeller. Another alternative, just holding back the controls during the balloon, can result in a stall from an ‘unsuitable’ height above the runway, leading to a (very) heavy landing, which could damage the landing gear or worse.
How about a bit of floating?
Next reason why too much speed is dangerous: even if you flare correctly without ballooning, the aircraft is still going too fast to land. Instructor: “Just try to skim the runway; don’t let the aircraft land; try to keep it flying as long as you can, slowly pulling back on the controls until the aircraft slows and the main wheels touch down”. This is all absolutely fine, unless you are carrying excess speed, in which case you’ll end up flying a long way down the runway before you touch down. And skimming along the tarmac (or grass) at relatively slow speed for a few hundred meters at just a few feet of height is tricky enough for an experienced airshow pilot, let alone a novice just trying to get back to terra firma. Throw in some cross wind, and/or a gust or two, and the risk of disaster rises exponentially! After a period of ‘skimming’ without landing, there is a huge temptation to let the nose drop a bit (or worse, push it down), just to get the wheels on the runway, and this can have two potential results: (a) because you’re still going too fast, the nose wheel touches down first and you’ll bounce/balloon, or (b) the impact will bend the nose leg and maybe bust the prop – if you’re lucky.
There are remedies for both ballooning and floating after they start but the easiest solution is not to let them happen at all!
Calculating the correct threshold speed
Which is where we get back to speed. There’s a GA rule of thumb about landing speed over the threshold. This says you should aim for about 1.3 times stall speed in landing configuration. As an example, with a stall speed of 45 knots the aim is (technically) 58.5 knots over the threshold – which is usually rounded to 60 knots. With low-inertia light sport aircraft, which have lower landing speeds, it’s probably safer to go for about 1.75 times stall speed, as wind gusts can be a much higher proportion of approach speed. So, for a stall speed of 27 knots (A32 Vixxen) the threshold speed should be about 47 knots – which is exactly what the pilot manual gives. Note – this is 20 knots ABOVE the stall speed!! If you come in at 55-60 knots over the threshold, you are flying about twice as fast as the stall speed – no wonder the aircraft is difficult to land!
What a drag
There are big differences in drag between aircraft. And drag affects how quickly the aircraft slows down when you throttle back for landing. The more the drag, the quicker the aircraft will slow down and vice-versa. To some extent, high-drag aircraft are easier to land than their more slippery siblings. As you cut power and round out to land, they will slow down more quickly, so if you are a few knots over the correct speed, they will help you out by slowing quickly. However, the more slippery the aircraft, the more accurate you need to be with the threshold speed; this is because if you are faster than you should be, the speed will not wash off quickly and ballooning and floating become much more likely.
As a comparison, our A22LS Foxbat is much much draggier than the A32 Vixxen. This is clearly evidenced in the fuel economy and the extra 20knots at cruise speeds. While the book figures for landing threshold speeds are much the same at 49 knots, coming in at 55 knots in the Foxbat will still allow you a reasonably easy landing. Try it in the Vixxen and because of its low-drag airframe, you’ll probably do a lot more floating. Add yet another 5 knots ‘for safety’ and even the Foxbat will take a while to land and the Vixxen will take you all the way down the runway into the fence at the end.
Landing weight
There’s an important additional piece of information needed here – the landing weight of the aircraft. All manufacturers quote stall speeds at maximum gross weight – for light sport aircraft, this is 600 kgs. If the stall speed is 28 knots at 600 kgs, it will be noticeably slower at (eg) 450 kgs actual weight, which in an A22LS Foxbat equates to the aircraft with one pilot and 50 kgs (70 litres) of fuel. In fact, it could be as much as 3-4 knots slower. Re-calculating the approach speed for this weight: (eg) 25 kts x 1.75 = 44 kts.
Hopefully, instructors teach their students properly about the difference weight can make to stall – and thus landing – speeds. This is particularly important for light sport aircraft, where the pilot, passengers, fuel and baggage make up a much bigger proportion of the weight and therefore have a much more significant effect on speeds than heavier GA aircraft.
Wind
Finally, a point about wind. I’ve often heard it said you should add 5-10 knots to your approach speed if the wind is across the runway and/or gusty. The idea being that if the wind suddenly drops during your approach, the aircraft is still going fast enough to keep flying above stall speed. In heavier GA aircraft, this may well be valid, as using the throttle to regain speed to arrest the momentum of a sudden descent takes time. However, modern light sport aircraft are much more responsive to throttle than their older GA counterparts, so I would never add more than 5 knots to the ‘book’ approach speed in a cross or gusty wind and use the throttle to stop descent quickly if a sudden drop occurs due to a gust.
In summary – read the pilot manual for your aircraft to check the threshold speed for that specific type – do not rely on rules of thumb, like “all aircraft are OK at 60 knots” down final and over the threshold. If the manual gives 49 knots at gross weight stick to it and – if it’s a light sport aircraft – even a bit slower if you do not have a passenger and/or lots of fuel. If you don’t stick to the book speeds, you are looking for trouble and for sure, you’ll end up ballooning or floating and sooner or later you’ll bend something. Hopefully, not yourself or your passenger!
5 easy steps to change your Foxbat/Vixxen oil
Here’s how to change the oil and filter on your Aeroprakt A22LS Foxbat or A32 Vixxen Rotax 912ULS engine:
1. Prepare for your oil change.
Make sure you have the following items ready:
A copy of the current Rotax Line Maintenance Manual for your engine. Whatever else follows, you should observe the requirements of this manual!
Three litres of suitable oil – we recommend Shell Sport Plus 4 oil as it is compatible with both unleaded and leaded fuel.
A Rotax approved replacement oil filter canister.
A fresh copper sealing ring for the oil reservoir drain plug.
Lock-wire and lock wire pliers.
A pair of side-cutters to remove old lock-wire.
18mm spanner and 17mm spanner or socket to remove the oil reservoir drain plug.
16mm spanner or socket to remove the magnetic plug on the side of the engine near the oil filter. NB> Older engines may have either a hex key or torx socket – check yours first!
Torque wrench which covers the range 25Nm
A suitable oil filter canister removal and replacement tool.
Ideally, a cutting tool to open the old oil filter to check for metal residues. If you don’t have one but know a friendly LAME or L2, they might lend you one.
A large container or bucket (with at least a 5 litres capacity) to collect the old oil.
Some kind of clean funnel to help you refill the reservoir with new oil.
Plenty of old rags to mop up spilt oil.
Then thoroughly warm up the engine – ideally go for a couple of circuits or a 20-minute flight – to ensure the oil is hot and fluid. Do not run the engine inside your shed/hangar!
2. Drain the oil and remove the old filter
The following actions should be completed in a timely fashion, to avoid oil draining out of the hydraulic valve lifters and oil lines. Do not drain the oil and leave (eg) overnight before refilling the next day.
After warming the engine, remove the top and bottom engine cowlings. Keep the cowling screws in a safe place. Take off the oil reservoir cap and ‘burp’ the engine several times to ensure all the sump oil is transferred to the reservoir.
Place an old oil bucket under the reservoir. Cut off and remove the drain plug lock-wire. Holding the captured nut on the reservoir with a 18mm spanner, use a 17mm spanner to loosen the drain plug. Carefully unscrew the drain plug and remove it together with its copper sealing washer. WARNING! The oil is HOT! Be careful not to drop the drain plug into the oil bucket! Allow at least 15 minutes for the oil to drain out. Remove the old copper sealing ring on the plug and replace with a new one – set the drain plug aside ready for reinstallation. DO NOT MOVE THE PROPELLER WHILE THERE IS NO OIL IN THE ENGINE!
While you are waiting for the oil to drain, place plenty of rags or a piece of cardboard under the oil filter to stop oil dripping on to the coolant radiator underneath. Loosen and remove the old oil filter. It contains quite a bit of oil, so remove it as quickly as you can to minimise drips etc onto the coolant radiator. Any oil on the radiator will be blown all over the engine bay when you restart the engine, so it’s important to keep it as clean as possible!
Cut and remove the lock-wire and unscrew the magnetic plug in the side of the engine just above the oil filter, using a 16mm spanner.
3. Inspections and records
Check the magnetic plug for metal accumulation per the Rotax Maintenance Manual. Some build up of metal particles is acceptable, particularly when the engine is new, as the oil lubricates the gearbox as well as the engine itself. See the Rotax manual for details of acceptable and unacceptable amounts of metal residue. Take a photo of the plug with any metal residue attached and date it for future reference in case you need it for comparison.
Clean up the plug with a cloth and some clean fuel and replace it – tighten to a torque of 25Nm. DO NOT OVER-TIGHTEN – remember, this is an aluminium crank case and the steel plug can damage the threads if you use too much brute force. Lock-wire the plug, making sure you replace this correctly so that the plug is held tight in the correct sense and cannot come loose!
Cut open the filter canister with a suitable tool and extend the paper oil filter on the bench to its full length. Carefully inspect the filter paper on both sides to identify any excessive metal residues. Check the Rotax manual for details of what is acceptable. Ideally, fold up the filter paper and keep it in a sealed and flight time/dated plastic bag in case you need it for reference at some later date.
4. Refill with new oil and install a new filter
Clean the oil filter contact face on the engine and install the new oil filter canister per Rotax instructions. Smear some fresh engine oil on the rubber washer/seal in the new filter and screw it back in place by hand. After tightening by hand as much as you can, further tighten the filter by rotating about 270 degrees (¾ of a turn). DO NOT OVER-TIGHTEN! Wipe away any oil spills around the bottom of the filter.
Some people like to dab a drop of coloured paint (nail varnish is excellent for this) on the oil filter and housing so you can see at a glance if it has started to unscrew.Clean the area around the oil reservoir drain and re-install the drain plug with its new copper sealer/washer. Hold the captive nut on the reservoir with a spanner and use a torque wrench to tighten the drain plug to 25Nm. Re-lock-wire the drain plug in place. Make sure you do this correctly so that the plug is held tight in the correct sense and cannot come loose!
Fill the oil reservoir with 3 litres of fresh oil. Ensure the ignition is switched off and hand-crank the engine about 20 turns of the propeller (in the correct sense, never backwards!) to help refill the complete oil system. Make sure you replace the oil reservoir cap!
5. Finishing up
Remove and/or put away/dispose of all the old oil, filter, tools etc. Don’t replace the engine cowlings yet.
Pull the aircraft out of the hangar and ensure it’s well away from anything loose that might get sucked into the prop.
Get in and start the engine. Watch the oil pressure gauge to ensure the oil pressure is rising within 10-20 seconds. If not, shut down. Check there is oil in the reservoir. Ensure all switches including ignition, are OFF and, using the propeller blades, hand-crank the engine for 5-10 rotations of the propeller. Restart the engine and adjust to around 2300-2500 rpm.
If the pressure still does not rise within 10-20 seconds, shut down and carry out a full check of the oil system to ensure there are no loose hoses and that you did actually refill the oil reservoir!
If the pressure rises OK, run the engine for about 15 minutes at various rpm until it is well warmed through. Shut down and check for oil leaks – particularly round the oil filter, magnetic plug and reservoir drain plug.
If all is OK, replace the engine cowlings and you’re ready for the next flight!
Side-slipping in the A32 Vixxen
The A32 Vixxen (and A22 Foxbat/Kelpie) can be freely side-slipped with or without flap. Pilots should read the Pilot Operating Handbook (POH) carefully, as the information on side-slipping speeds and bank angle limit is all there.
In summary for the A32 Vixxen: the limit for full control deflection is 81 knots – this is the top speed limit for side slipping with no flap.
The flap limiting speed is 79 knots and this is the top speed limit for side slipping with flap. Technically, there is no bottom speed limit for side slipping but be strongly aware of stalling at slow speeds with large control surface deflections. Stall speeds will be higher than in normal straight & level flight!
Finally, the maximum bank angle for slips is 15 degrees.
Personally, my preference for side slipping speed is somewhere between 50 and 65 knots, with or without flap. Everything seems more comfortable and controllable at these speeds, which are well above the stall and don’t stress the airframe to its maximum limits.
Make sure to check out video about side slipping